Predictive Maintenance statt Pannendienst
Smarte Sensoren und Künstliche Intelligenz können drohende Ausfälle frühzeitig voraussagen
Die Uptime, sprich die Einsatzfähigkeit und Verfügbarkeit mobiler Arbeitsmaschinen, möglichst hochzuhalten, gehört zu den wichtigsten Anforderungen im Off Highway-Bereich. Dies wird auch im Rahmen der SYSTEMS & COMPONENTS, die vom 9. bis zum 15. November zeitgleich mit der AGRITECHNICA stattfindet, zu einem zentralen Thema. Condition Monitoring, Ferndiagnose und Predictive Maintenance zählen zu den bestimmenden Themen auf dem Messegelände. Gezeigt werden in Hannover Lösungen, die dank intelligenter Sensoren und Datenanalysen rechtzeitig auf Störungen aufmerksam machen – Instandhaltungsmaßnahmen werden so planbar und Nutzungsreserven von Verschleißteilen besser erschlossen.
Für die schweren Aufgaben auf dem Acker oder der Baustelle sind sie unentbehrlich: Off-Highway-Maschinen. Die extremen Einsatzbedingungen erfordern Komponenten, die höchsten Belastungen standhalten. Doch früher oder später kommt der Punkt, an dem Verschleiß auftritt. Oftmals registriert der Fahrer in der Kabine die Abnutzungserscheinung zu spät. Jeder Schaden an den Fahrzeugen bedeutet teure Reparaturen und lange Standzeiten, weshalb die klassischen "Run-To-Failure"-Prozeduren der reaktiven Instandhaltung hier an ihre Grenze stoßen. Prävention lautet folglich das Motto auf dem Messegelände in Hannover.
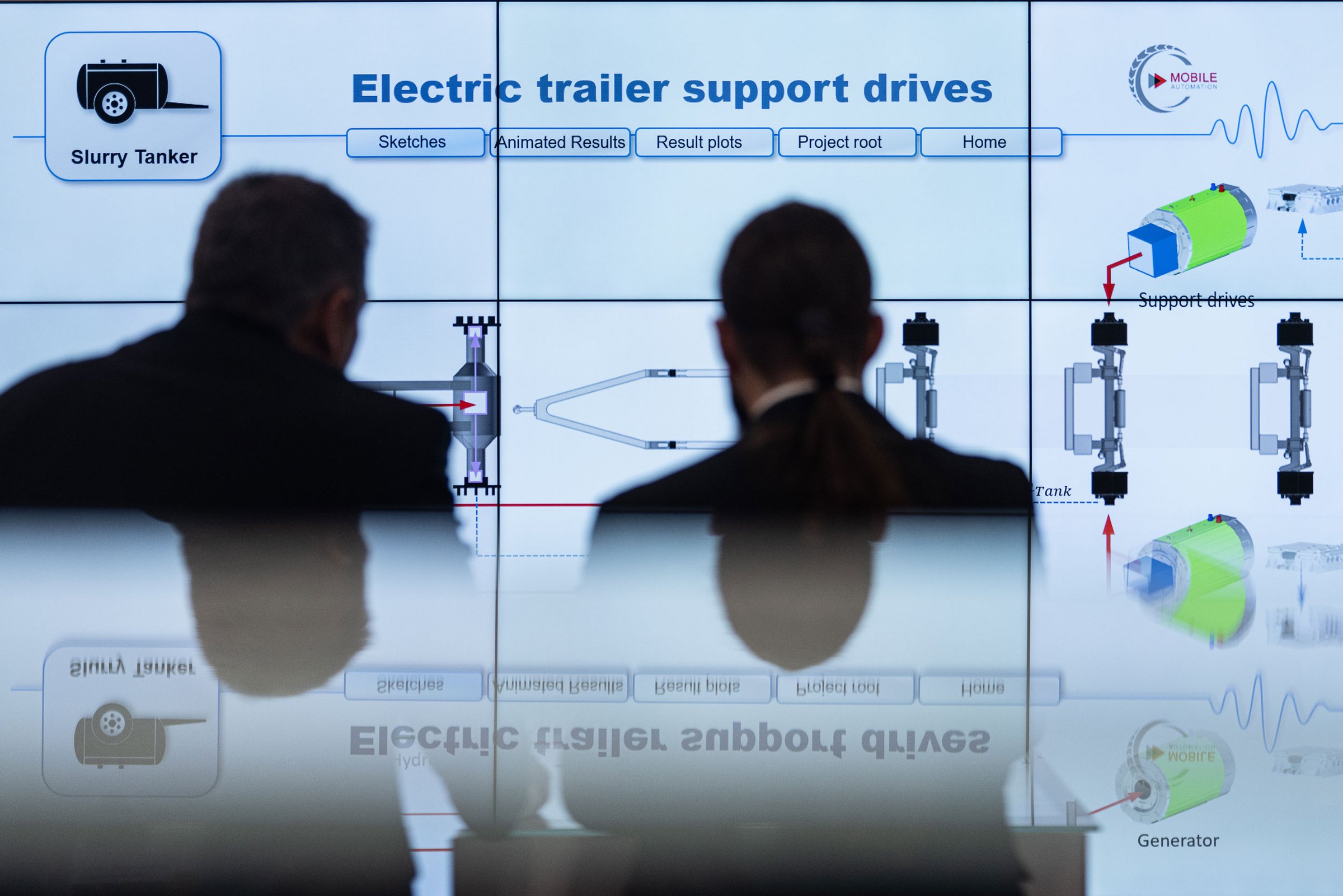
„Störungen und Defekte im Vorfeld erkennen und Wartungsmaßnahmen zeitnah ergreifen – das sind nicht nur für Landmaschinenhersteller, Lohnunternehmer und Landwirte ausschlaggebende Faktoren, um effizient zu arbeiten“, sagt Petra Kaiser von der DLG (Deutsche Landwirtschafts-Gesellschaft). Predictive Maintenance, also die Kombination aus moderner Sensorik und Echtzeit-Datenanalyse, die aus aktuellen und historischen Daten mittels Algorithmen voraussagt, wann ein Schadensfall eintritt, hilft auch auf der Baustelle, den perfekten Instandsetzungszeitpunkt festzulegen. „Die in Hannover ausstellenden Unternehmen arbeiten mit Hochdruck an Lösungen, die auf vorausschauenden Instandhaltungsstrategien basieren und Störungen an der Mechanik, Hydraulik, Elektrik und Elektronik lokalisieren, bevor diese kostspielig zu Buche schlagen“, so die Brand Managerin der SYSTEMS & COMPONENTS. Stets im Blick sind dabei die Gesamtbetriebskosten des Fahrzeugs über die Nutzungsdauer, die Total Cost of Ownership (TCO). Neben dem Nutzen für die Kunden entfalten die mittels Monitoring- und Diagnose-Apps gewonnenen Informationen auch im Engineering, Vertrieb und Service ein großes Nutzenpotenzial. So lässt sich beispielsweise das Design der Maschinen – lange bevor diese gebaut werden – anhand realer Lastkollektive und Nutzungsdaten optimieren.
Maschineninformationen in Echtzeit
Ein wichtiger Treiber der Entwicklung von Predictive Maintenance Systemen im Off Highway-Bereich ist die Digitalisierung. Sie ermöglicht es, große Mengen an Informationen aus verschiedenen Quellen entlang des gesamten Antriebsstrangs zu erfassen und zu analysieren. Smarte Sensortechnologien erweitern die verfügbare Datenbasis, während rechenstarke Telematikeinheiten mit zahlreichen Schnittstellen für eine sichere Datenübertragung bei anspruchsvollen Einsatzszenarien sorgen. Die Aussteller der SYSTEMS & COMPONENTS haben sich den Herausforderungen in Landwirtschaft, Forst- und Bauwesen sowieund Bergbau angenommen und bieten Systeme, die trotz widriger Bedingungen höchste Diagnosezuverlässigkeit versprechen.
Im Fokus des Condition Monitorings stehen unter anderem Vibrationsmessungen. Werden sie an der laufenden Maschine durchgeführt, sind sie eine effektive Methode für eine rechtzeitige Verschleißerkennung an Gelenkwellen, Wälzlagern, Getrieben oder Motoren. Der Einblick, den die Daten gewähren, reicht bis tief in die System- und Komponentenebene der Fahrzeuge. Die Sensoren erfassen die Beanspruchungen und Materialermüdungen direkt an den aussagekräftigen Stellen. Ob die Drehmomentmessung in Wellen der Haupt- oder Nebenantriebsstränge oder die Zugkrafterfassung in Kraftmessbolzen – viele der drahtlosen Lösungen, die in Hannover vorgestellt werden, zeichnen sich durch ihre anwendungsfreundliche Plug-&-Play-Philosophie aus. Mit einer individuell auf die Anforderungen abgestimmten Kombination aus IIoT-Sensoren, Gateways und Cloud-Services steht auch einer nachträglichen Integration in die Systemarchitektur der Maschinen nichts im Weg.
Sensoren für den Einsatz im Harsh Environment
Smart, integriert und remote sind die Sensoren kleine Helfer mit großer Wirkung. So stellen sie neben ihrer Grundfunktion, der Erfassung einer Messgröße, weitere Informationen sowie Handlungsempfehlungen zur Verfügung – beispielsweise als Variante mit zusätzlicher Blackbox-Funktion, aus der bei Bedarf Historiendaten abrufbar sind. Oder als Sensor, welcher basierend auf Algorithmen bereits erste Handlungsempfehlungen an den Fahrer in der Kabine gibt. Dadurch lassen sich die Systeme auch in Umgebungen ohne Datenverbindung autonom einsetzen, beispielsweise in Minen. Mit ihnen lässt sich genau vorhersagen, wann die nächste Instandhaltung fällig wird. Das macht die Wartungsplanung einfacher, weil sie zeitlich besser auf Inspektionen abgestimmt werden kann.
Zu den jüngsten Innovationen zählen elektronische Sensoren für Baumaschinen, die über den Verschleißzustand des Kettenlaufwerks in Echtzeit informieren, ohne dass eine Kettengliedmessung nötig ist. Zum Einsatz kommen sie serienmäßig bei den Cat Dozern mit einem HD-XL-Laufwerk der Baureihe D5, D6 und D8 sowie bei den Cat Kettenladern 953 und 963. Der Sensor wird dabei gesichert im Kettenglied installiert, sodass Stoßbelastungen ihm nichts anhaben können. Beide Kettenstränge sind mit einem solchen intelligenten Kettenglied ausgestattet; so verfügt jede Maschine über zwei Sensoren. Bei einem Verschleißrichtwert von 40 Prozent wird eine erste Sichtung des Laufwerks empfohlen. Erreicht der Verschleißwert 100 Prozent, wird ein Austausch nötig. Über 2.000 Cat Maschinen wurden bislang mit der Technologie ausgestattet. „Aktuell sind über 60 davon deutschlandweit im Einsatz“, bestätigt Andreas Kurz, Senior Produktmanager Laufwerke bei der Zeppelin Baumaschinen GmbH. Ein Sensor habe auch schon ausgelöst, „wodurch ein Maschinenausfall sowie eine Reparatur verhindert werden konnte.“
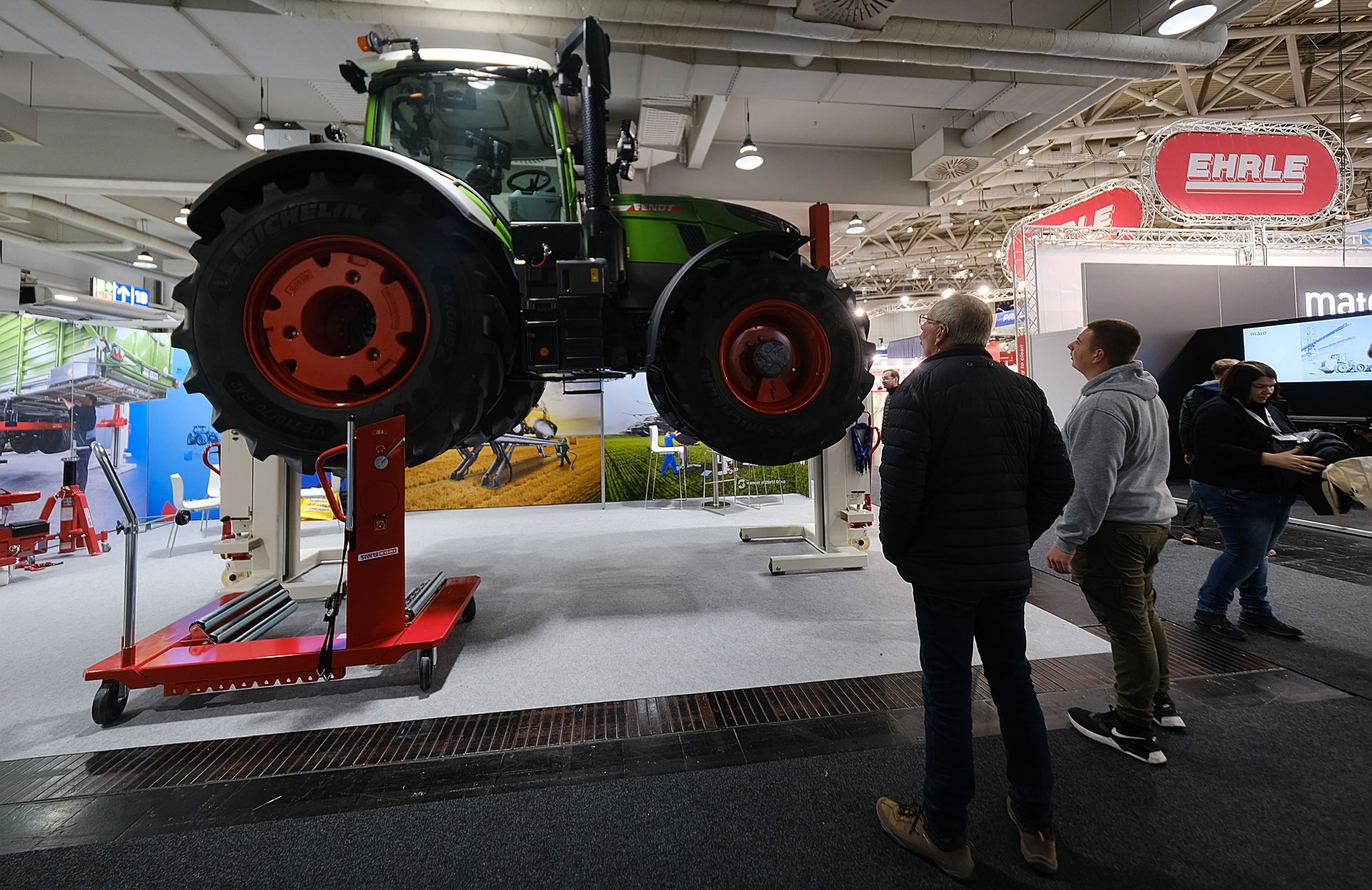
Instandhaltung trifft auf Künstliche Intelligenz
Sind die Hausaufgaben unter der Haube gemacht, das heißt: eine zukunftssichere Telematic Control Unit (TCU) ausgewählt, die Sensoren und die Software für eine effiziente Datensammlung und -übertragung implementiert und das Device-Management in trockenen Tüchern – einschließlich Remote Diagnose und Monitoring, kann es mit der vorausschauenden Instandhaltung losgehen. Nun gilt es, die Daten aufzubereiten und zu visualisieren. Auch wenn beim Condition Monitoring der Zustand von Maschinen mithilfe von Sensordaten bereits überwacht wird: Wirklich vorausschauend – ganz im Sinne von Predictive Maintenance – wird diese zustandsbasierte Instandhaltung erst dann, wenn Künstliche Intelligenz ins Spiel kommt.
Das Prinzip der vorausschauenden Wartung ist dabei ebenso logisch wie komplex. Die von Sensoren in Echtzeit gesammelten Daten werden mit weiteren Quellen verknüpft, etwa mit Erfahrungsdatenbanken, Pannenstatistiken und Nutzungsmustern. Mit Hilfe entsprechender Algorithmen und unter Einbeziehung von Künstlicher Intelligenz lassen sich so Muster und Trends erkennen, welche frühzeitig auf einen anstehenden Wartungsbedarf hinweisen.
Digitale Zwillinge blicken weiter voraus
Als internationaler B2B-Treffpunkt zeigt die SYSTEMS & COMPONENTS nicht nur neueste Technologien, sondern ermöglicht auch den fachlichen Austausch und die Diskussion zentraler Zukunftsthemen. Dass die datengetriebenen Prognosemodelle der vorausschauenden Instandhaltung zunehmend an Bedeutung gewinnen, zeigen auch die Expertenvorträge, die im Rahmen der Expert Stage SYSTEMS & COMPONENTS unter dem Leitthema "Digitale Services" gehalten werden. Da diese Trends aber anhand vergangener Ereignisse extrapolieren, fehlt es an Daten zu Ausfallszenarien, die bis dato nicht aufgetreten sind.
Eng verknüpft mit der Thematik Predictive Maintenance ist deshalb der digitale Zwilling (Digital Twin): die virtuelle Kopie beziehungsweise Simulation einer mobilen Arbeitsmaschine beziehungsweise ihrer verbauten Komponenten. Mit ihm sollen sich auch Ausfälle simulieren lassen, die in der Historie noch gar nicht aufgetreten sind. Für Petra Kaiser von der DLG zählen digitale Zwillinge deshalb zu den Schlüsselinnovationen im Off Highway-Sektor. „Die Anforderungen an mobile Arbeitsmaschinen in der Land- und Bauwirtschaft sowie im Bergbau steigen kontinuierlich. Mittels vorausschauender Instandhaltung lassen sich Produktivitätssteigerungen erzielen, die sonst unmöglich wären“, so die Brand Managerin. Anschaulich wird dies vom 9. bis 15. November auf dem Messegelände in Hannover, wenn sich die Technologiespezialisten rund um die Automatisierung und Vernetzung mobiler Arbeitsmaschinen auf der SYSTEMS & COMPONENTS präsentieren.