Predictive maintenance instead of breakdown service
Smart sensors and artificial intelligence can predict imminent failures early
Maximizing uptime—ensuring that mobile machinery remains fully operational and available—is one of the top priorities in the off-highway equipment sector. This will be a central theme at the Systems & Components event, held from November 9 to 15, 2025, alongside the AGRITECHNICA trade fair. Condition monitoring, remote diagnostics, and predictive maintenance are among the key topics at the exhibition. Solutions will be presented in Hanover that, thanks to intelligent sensors and data analysis, alert to disturbances early, making maintenance measures easier to plan and optimizing the use of wear parts.
Off-highway machines are indispensable for heavy-duty tasks in the field or on construction sites. The extreme operating conditions require components that can withstand the highest loads. However, sooner or later, wear occurs. The in-cab operator often notices the signs of wear too late. Each damage to the vehicles means expensive repairs and long downtimes, which is why the classic "run-to-failure" reactive maintenance procedures reach their limits here. Prevention is therefore the key theme at the exhibition grounds in Hanover.
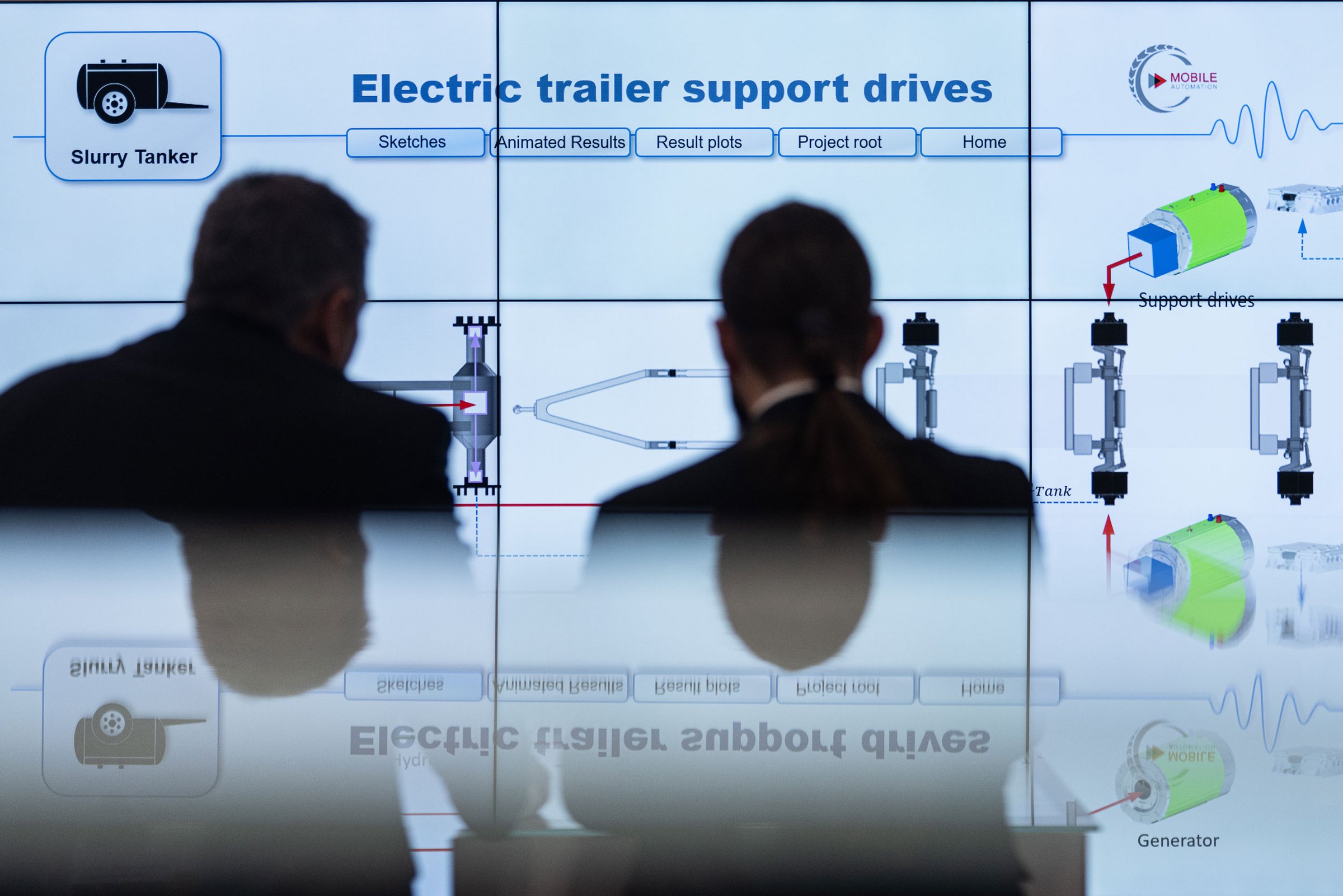
“Detecting faults early and taking timely maintenance measures are crucial for efficiency—not just for agricultural machinery manufacturers, but also for contractors, and farmers,” says Petra Kaiser, Brand Manager of Systems & Components, the DLG (German Agricultural Society). Predictive maintenance, the combination of modern sensor technology and real-time data analysis, uses algorithms to predict when a failure will occur, based on current and historical data. This helps determine the perfect repair time for construction site machinery.
"The exhibiting companies in Hanover are working intensively on solutions based on predictive maintenance strategies that localize faults in mechanics, hydraulics, electronics, and electrical systems before they result in costly damage," says Kaiser. Always in focus is the total cost of ownership (TCO) of the vehicle throughout its service life. In addition to customer benefits, the information gained through monitoring and diagnostic apps also has significant potential for engineering, sales, and service. For instance, machine designs can be optimized long before production using real load spectra and usage data.
Machine information in real time
A key driver of the development of predictive maintenance systems in the off-highway sector is digitalization. The technologies from this field enable the collection and analysis of large amounts of data from various sources along the entire drivetrain. Smart sensor technologies expand the available data base, while high-performance telematics units with multiple interfaces ensure secure data transmission in demanding operating conditions. The exhibitors at Systems & Components have taken on the challenges in agriculture, forestry, construction, and mining, offering systems that promise high diagnostic reliability even under adverse conditions.
Sensors for use in harsh environments
Smart, integrated, and remote—these sensors are small helpers with a big impact. In addition to their core function of measuring physical values, they provide additional information and recommendations for action. For example, sensors that give the operator initial recommendations based on algorithms. These systems can operate autonomously in environments without data connections, such as in mines. With these capabilities, maintenance needs can be predicted with great precision, simplifying service planning and aligning it better with inspection schedules. Recent innovations include electronic sensors for construction machinery that monitor the wear status of undercarriage track systems in real-time, without the need for manual track link measurements
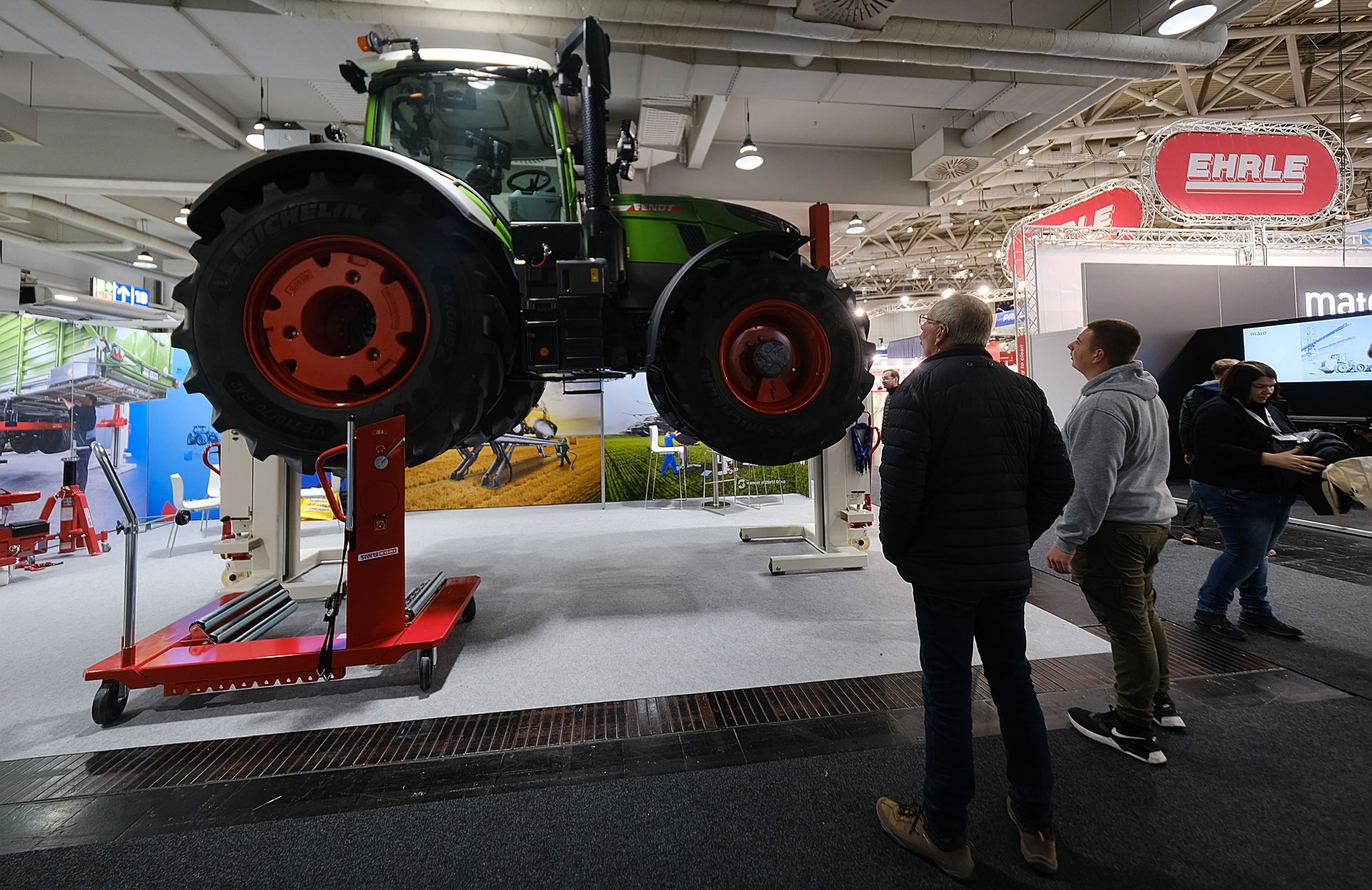
Maintenance meets artificial intelligence
Once the groundwork is done under the hood: A future-proof telematic control unit (TCU) has been selected, the sensors and software for efficient data collection and transmission have been implemented, and device management— including remote diagnostics and monitoring—is secured, predictive maintenance can begin. The next step is to process and visualize the data. Even though condition monitoring already supervises the condition of machines with sensor data, this condition-based maintenance only becomes truly predictive, in the sense of predictive maintenance, when artificial intelligence is brought into play.
Digital twins look further ahead
As an international B2B platform, Systems & Components not only showcases the latest technologies but also facilitates expert exchange and discussion of central future topics. The increasing importance of data-driven forecasting models in predictive maintenance is also demonstrated by expert presentations that will be held as part of the Expert Stage of Systems & Components, under the overarching theme of "Digital Services". However, as these trends are extrapolated based on past events, there is a lack of data on failure scenarios that have not yet occurred.
Closely linked to predictive maintenance is the digital twin: the virtual replica or simulation of a mobile machine or its installed components. It allows the simulation of failures that have not yet occurred historically. This makes it possible to predict maintenance needs proactively, even for scenarios not previously encountered.
“The demands placed on mobile machines in agriculture, construction, and mining are continuously increasing. Predictive maintenance allows for productivity gains that would otherwise be impossible,” concludes Kaiser. This will be clearly demonstrated from November 9 to 15 at the exhibition grounds in Hanover when technology specialists in the automation and networking of mobile machinery will present their solutions at Systems & Components.